How To Reduce Maintenance Costs Through Proactive Decision Making
Every business that wishes to maintain its position as a market leader must work to boost profitability. Profitability by far is one of the most important aspects of any business. When it comes to the process industries, it is not unusual for senior management to frequently turn to cut operating costs in the pursuit of increased profits.
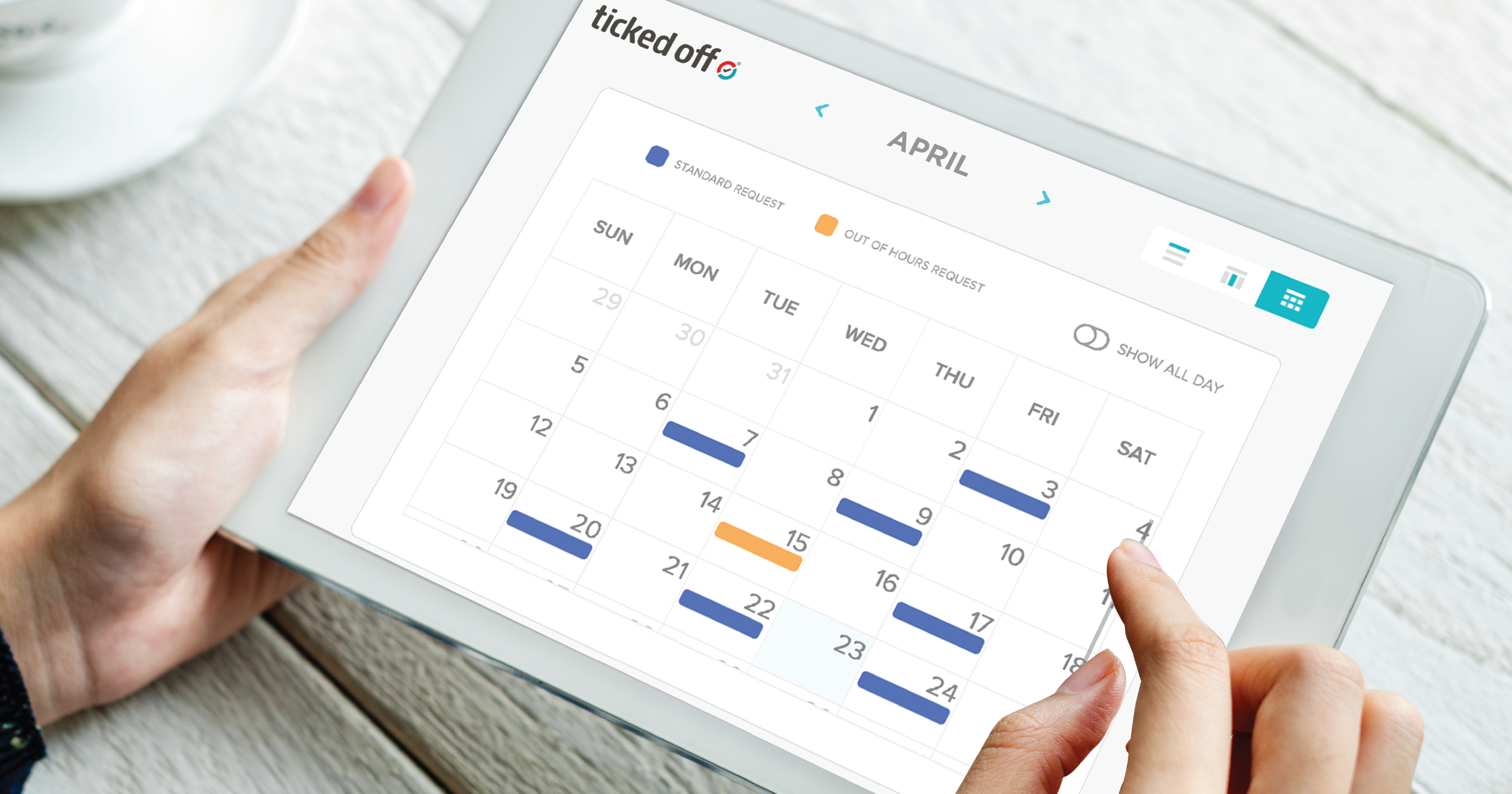
Every business that wishes to maintain its position as a market leader must work to boost profitability. Profitability by far is one of the most important aspects of any business. When it comes to the process industries, it is not unusual for senior management to frequently turn to cut operating costs in the pursuit of increased profits.
Considering that the majority of managers and executives still solely view maintenance as a cost centre, cutting operating expenses in the maintenance division is frequently at the top of their priority list. The drive to better optimize maintenance operations puts a lot of burden on maintenance managers and even contractors.
The only certain way to permanently lower maintenance costs is by controlling them with software that immediately implements visibility and context.
Techniques for maintenance that lower operational costs
All maintenance monitoring aims to increase the efficacy and efficiency of your maintenance activities, which lowers operational costs.
Although this is the case, a recent survey reveals that over 50% of businesses still heavily rely on reactive maintenance as part of their overall maintenance strategy. Reactive maintenance should only have a small place in your maintenance approach and rather, it should simply play a supporting function and defer to more effective maintenance operations for the heavy lifting.
High or increasing reactive maintenance costs are always a red flag that software is required to give visibility into upcoming maintenance activities.
Predictive Maintenance
Although preventive and predictive maintenance (PdM) have similar objectives, they are executed very differently. The goal of predictive maintenance is to foresee equipment failure before it happens. As with regular maintenance, predictions are not based on the typical life cycles of the machinery.
Some predictive maintenance tactics focus on physical inspection of the relevant equipment but adopting a software system as a watchful eye over operations and to track facilities will yield the best results.
Prospective failures will start to form patterns and give insights into your equipment's or building’s present functioning health by measuring maintenance activity. This will help you avoid unplanned breakdowns or outages.
Preventive Maintenance
A preventive maintenance strategy is the most common method of maintenance. It's not a coincidence because when properly implemented, it has been demonstrated to provide a high return on investment over time, and reinstalling broken equipment or performing building maintenance is simpler than that of any other proactive maintenance technique.
A preventative maintenance strategy should be considered for implementation by any company with more than one location or a medium to large location. Although switching from reactive to preventative maintenance will take some time without software, reducing costs can only be achieved through this process.
Reliability-Centred Maintenance
An extremely complicated approach to maintenance is reliability-centred maintenance. The major objective is to pinpoint every machine's potential failure mode before creating a unique maintenance plan for each piece of machinery.
It is complicated, but it can be effective.
Since a thorough study of many maintenance items is required, this can be a challenging undertaking for any organisation. Reliability-centred maintenance needs routine data collecting from the machine, store, preventative and predictive maintenance strategies, and routine basic inspections of all the installed equipment and buildings because it is an advanced maintenance plan. It is almost impossible without software to monitor and provide visibility into breakages and downtime.
Reliability-centred maintenance can be used for both small and large systems, although it can be challenging to identify failure modes and distinguish between various system components. Implementing business and asset maintenance software can free up time for a maintenance manager to research more specific instances of best practice upkeep. Prioritising failure modes should come after a company has identified its production assets that are essential to its operations.
The proper categorisation of assets is essential in this maintenance type because a reliability-centred maintenance approach does not deal with functionality but rather reliability.
Using maintenance software to cut operating costs
Without the aid of suitable maintenance software, implementing a more preventative maintenance strategy is all but impossible. Implementing appropriate and specialist software is the next most logical step.
A maintenance schedule's effectiveness must be based on accurate and trustworthy information. Using a mix of manual tools such as spreadsheets, emails, chat apps, and phone calls can never provide the context required for decision-making for proactivity. Without a central hub of information that enables you to create data-driven strategies, it is simply impossible to track all of the necessary information given the number of moving pieces.
As such, we must mention computerised maintenance management systems (CMMS) while talking about the reduction of operating costs because these software’s primary goal is to give you priceless and useful insights to optimise your entire maintenance process.
Lowering the cost of maintenance
Choosing which maintenance technique to concentrate on can be difficult because each has advantages and disadvantages. How do we know that one of the current maintenance approaches isn't uniformly better than the others?
Your business ultimately determines which maintenance strategies will be the most profitable. Since it is clear that not all successful businesses maintain their facilities in the same way, it is important to choose software that provides flexibility – of process, of workflow, of permissions, and of customisation to your specific requirements.
In an ideal situation, you would combine all tactics to achieve the best outcomes and save maintenance expenditure.
When all is said and done, one of the greatest ways to reduce costs that occur in your maintenance department is to choose the appropriate strategy (or a combination of techniques) and apply specialised software to manage the process, provide accountability, and provide visibility for decision-making.